Learn More About Heat Sealing
In its basic definition, heat sealing is the process of joining thermoplastic materials through the application of heat and pressure. As with all thermoplastic processing, heat sealing requires controlling three distinct variables: HEAT, TIME, and PRESSURE. Failure to control any of these variables can result in poor quality welds that peel or tear in use.
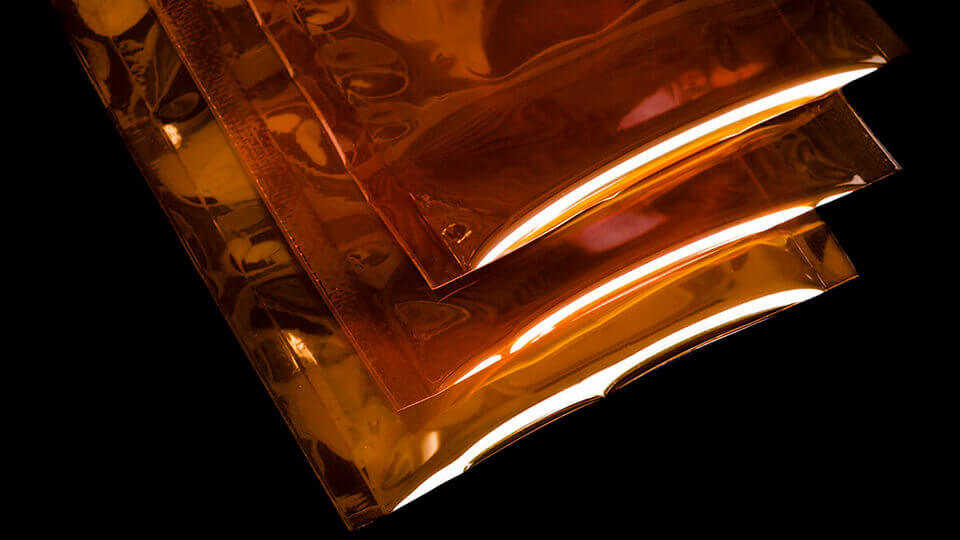
Common Types of Heat Sealing:
Thermal Impulse heat sealing employs a stationary element (Commonly refered to as a band or
ribbon) that heats and cools under pressure with every individual sealing cycle. The ability to
control the rate of heating, the time spent at the melt point, and the rate of cooling create
superior welds in thin thermoplastic films. Machines come in a variety of designs: Single ribbon,
dual ribbon, water cooled, but they all have ways to control heat, time, and pressure.
Employs heated platens that come in contact with the material being sealed. The material is heated
to the melt point under pressure and it cools unrestrained. Not having control of the cooling rate
results in excess shrinkage along the weld or deformation of the material as the platens are
opened.
Ultrasonic: Ultrasonic welding uses high frequency sound waves to produce heat by localized vibration. Parts are typically held together in a jig while they are heated creating the necessary pressure. Ultrasonic welding is typically used as a replacement to adhesives and solvents.
Ultrasonic: Ultrasonic welding uses high frequency sound waves to produce heat by localized vibration. Parts are typically held together in a jig while they are heated creating the necessary pressure. Ultrasonic welding is typically used as a replacement to adhesives and solvents.
Quality Heat Seal Requirements:
Material must reach the melt temperature of the polymer. Cooler sealing temperatures will produce
a poor weld that tends to peel , whereas overheating will cause degredation of the polymer and the
resultant loss of physical properties of the material. When bonding two dis-similar materials, the
heat must reach the melt point of the higher melting material, while not thermally degrading the
lower melting polymer.
The rate at which the materials reach the melt point, the amount of time they spend at the melt
point, and the rate of cooling are important factors to consider. Many materials are prone to
degradation when heated too fast. Too much time “In the melt” tends to cause thinning, especially
in materials that have low melt viscosities. Materials should be cooled to the point where they
can be handled without stretching or tearing.
Even pressure across the entire sealing surface must be achieved for a successful seal. Uneven
pressure can cause thinning and “Zipper” failure where the material thins at the edge of the weld
to the point where it tears away from the area of the weld. Uneven pressure also causes poor
transfer of heat from the platens to the material. Using the minimum pressure to force the melted
polymer together results in quality welds.
High Performance Film Custom Manufacturing